Case Study Fraunhofer
Requirements:
- Precise temperature distribution throughout inner chamber
- Variable humidity
- Easy to use
- Recording software
BINDER solutions:
- Temperature range: -10°C to 100°C
- Extended humidity range: 10% RF to 98% RH
- APT.line™ preheating chamber technology
- Humidity regulation with capacitive humidity sensor and steam humidification
- Inner chamber made completely of stainless steel
- BINDER Multi Management Software APT-COM™ basic edition
- Intuitive touchscreen controller with time-segment and real-time programming with internal data recording
- Internal data logger, measured values can be read out in open format via USB

For his master’s thesis, Siegfried Bähr chose both an exciting workplace as well as a challenging project. The young scientist wanted to use a BINDER climate chamber (KMF 115) to investigate how metallic powder materials interact with ambient humidity and the impact of this interaction for laser beam melting. Bähr, who originally hails from Munich, spent six months at the Fraunhofer Institute in Augsburg, Germany, in a quest to gain new insights. He subjected different powder materials to a range of climate conditions and observed the increase and decrease in moisture. “As we found out later, the process itself lasts only a matter of minutes,” Siegfried explains.
Bähr also wanted to uncover whether there was any link between the moisture in the powder material in its original state and the quality of the component later down the line. This, however, requires an understanding of what laser beam melting (LBM) actually is. LBM is currently the most commonly used method for the additive processing of metal powders. Here’s how it works: A thin layer of the powder material to be processed is applied to a construction platform. A continuous laser beam delineates the contour of the component. The powder melts completely and then solidifies, forming a rigid material layer. The construction platform is then lowered by the thickness of a single layer, a new layer of powder is applied, and the laser beam once again outlines the contour of the component. The process continues until all the layers have been generated and the finished component can be removed. All process data required by the equipment to produce the component, such as 3D CAD data, is collected in advance. Components produced in this way are being used more and more in key industries, such as air and space travel and the automotive industry. For example, certain engine manufacturers are batch-producing and installing engine parts made using additive manufacturing. However, before Bähr carried out the moisture tests using a BINDER humidity test chamber, he first wanted to get to know the characteristics of the equipment he was working with and was impressed by its performance: “The BINDER chamber is extremely effective. For example, it can approach test points that usually aren’t included, such as very low moisture levels combined with high temperatures. The chamber was able to maintain the same climate even under these conditions.”
Bähr adds: “The BINDER service team provided me with great support for any questions I had.” The low water consumption was also a point in BINDER’s favor according to the young researcher. He particularly enjoyed the simplicity with which the unit could be operated, saying “ I quickly felt at home with the Multi Management Software.”
As part of the experiments, Bähr also placed the powder samples in an aluminum dish, which was then placed on a set
of scales inside the chamber. The scales were positioned on an anti-vibration base plate, custom-built by BINDER for this very purpose. By recording the mass at certain intervals under a range of climate conditions, Bähr was able to dynamically record the increase in moisture in the powder. A number of recommendations for action when working with metal powders could ultimately be derived from the tests carried out by the young scientist. The investigations also revealed further insights into the subject of moisture in laser beam processing.
Bähr’s findings from his work at the Fraunhofer Institute will be made available to the wider industry.
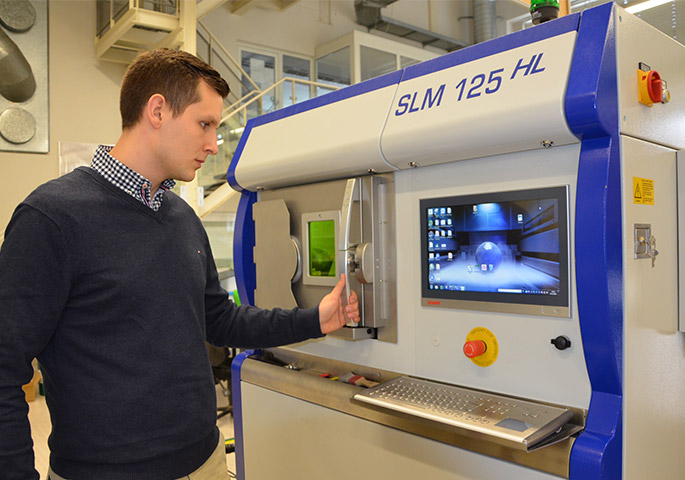

Advantages of constant climate chambers
- Homogeneous climate conditions thanks to APT.line™ preheating chamber
- Automatic water and waste water management
- Responsive steam humidification
- Large humidity range up to 98% RH
- Suitable for demanding stress tests with 85°C and 85% RH