Case Study Lapp gruppe
Tasks and objectives:
- Testing the functionality and service life of cables
- Aging behavior of plastic parts
- Ensuring product quality
- Quality testing and certification according to national and international standards
- Constant climatic conditions
BINDER solutions:
- ED and FD drying and heating chambers Classic.Line
- Tests with natural and forced convection
- Homogeneous temperature distribution even under full load
- High temperature accuracy
- Defined ventilation
- Easy-to-read program guidance
- Temperature range from 5 °C to 300 °C
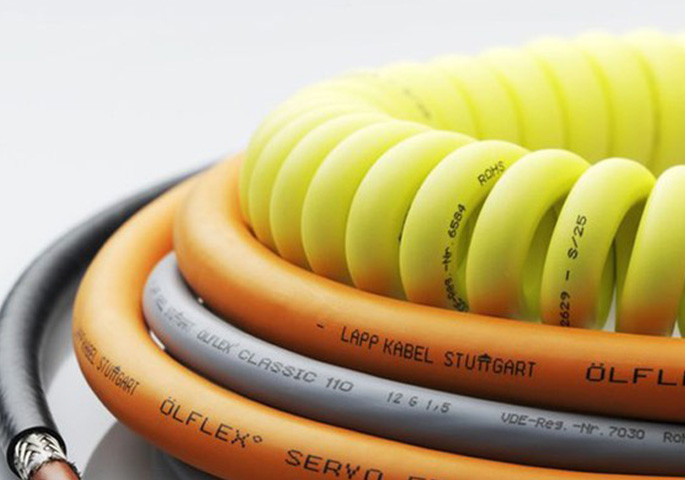
Plastic materials are subjected to rigorous testing in the laboratory.
“Maximum safety through comprehensive quality management” could be the slogan of the Lapp Group, one of the
leading providers of integrated solutions and brand products in the field of cable and connection technology. Ensuring
a consistently high product quality is clearly the company's top priority. A range of product features such as functionality or service life are highly dependent on the climatic conditions. Ever-increasing requirements are placed on the thermal resistance and the aging behavior of the plastic parts used – particularly in the field of cable and connection technology – as these must be able to function reliably without problems under extreme climatic ambient conditions. For example, heat can take its toll on the plastic jackets and insulation materials of the cables, making them age prematurely and become brittle. To determine how well a cable is going to last over the next decades, the Lapp Group rigorously tests the material. These tests significantly speed up the aging process.
Simulating artificial aging
25 different drying and heating chambers from the BINDER ED and FD series are used for this purpose. The quality tests and certifications are performed according to national and international VDE, UL, EN, ISO, and IEC standards. The thermal aging process of cable jacket materials is simulated in the test laboratory by exposing the materials to age accelerating conditions (temperature increase, high rate of air exchange). The artificial aging of products through controlled climatic conditions identifies their weak points and can predict material fatigue or even material failure. The acceleration effect is induced by varying temperature increases up to 300 °C. The tests are performed with both natural and forced convection. “Thanks to natural convection and the high rate of air exchange, all thermal processes in the ED series drying chambers are highly efficient,” explains Michael Hagenmüller, laboratory manager at Lapp. “The FD series drying chambers with forced convection are mainly used when we require rapid process dynamics.” Thanks to the APT.line™ technology, the chambers ensure a homogeneous temperature distribution across all levels even at full load.
“The BINDER chambers meet all requirements extremely reliably; they impress with a high temperature accuracy and precisely maintain the defined ventilation parameters in line with the time specifications,” says Michael Hagenmüller. “And the fact that they are excellent value for money was obviously another advantage.”
Global player
The Lapp Group, which is based in Stuttgart, has 17 manufacturing facilities worldwide and maintains its own research
and testing centers in Europe, Asia, and North America. It is active in approx. 100 countries with partner companies, and has 39 of its own distribution companies. The Group employs approximately 3,440 employees worldwide. Its core
market focuses on machine and plant engineering. Other important sales markets include the food, energy, mobility, and life science industries. The Group's portfolio includes cables and highly flexible cables, industrial connectors and screw technology, customer-specific assembly solutions, automation technology, and robotics solutions for Industry 4.0 and what is known as the smart factory.


Advantages:
- Temperature range: up to 300 °C
- Natural and forced convection
- Controller with LCD display
- Electromechanical control of the exhaust air flap
- Class 2 integrated independent adjustable temperature safety device (DIN 12880) with visual alarm
- Excellent temporal and spatial temperature accuracy