Case Study: BMC Racing Caronrahmen
Postawione zadanie:
- Suszenie i utwardzanie uformowanych rur karbonowych
- Suszenie i utwardzanie lakierów, nadruków oraz klejów montażowych
- Stabilny suchy klimat
- Stabilna wilgotność powietrza
- Niskie zużycie energii
- Niski poziom emisji ciepła
- Łatwa obsługa
Rozwiązania firmy BINDER:
- Komora temperaturowa FED z konwekcją wymuszoną
- Jednolite warunki temperaturowe
- Równomierna cyrkulacja powietrza dzięki sterowanemu cyfrowo wentylatorowi
- Szeroki zakres temperatury od 5 °C przez temperaturę otoczenia, aż po 300 °C
- Krótki czas nagrzewania
- Niski poziom emisji ciepła dzięki izolacji 60 mm
- Rozszerzone funkcje czasu

Karbon znajduje zastosowanie tam, gdzie niezbędna jest lekkość i stabilność. W szwajcarskim Grenchen powstają pierwsze na świecie ramy karbonowe do rowerów wyścigowych, wytwarzane automatycznie w technologii BINDER. W 2011 r. Australijczyk Cadel Evans wygrał Tour de France na rowerze wyścigowym BMC dzięki aktywnemu wsparciu kolegów z teamu, którzy na rowerze karbonowym z Grenchen mierzyli się z wyzwaniami najcięższego etapowego wyścigu świata. Technologia z innej galaktyki. Nazwano ją „Stargate”, bo to, co się dzięki niej wytwarza, wydaje się istotnie nieziemskie. Jej sekret tkwi w kole o średnicy większej niż człowiek z rozpostartymi ramionami. Służy ono do wytwarzania jednego z najmocniejszych i najlżejszych zarazem materiałów, jakie wymyślił człowiek: precyzyjnie wyplatany karbon – idealny do produkcji ram rowerów wyścigowych. „Stargate” to, dokładnie rzecz ujmując, zaawansowane technologicznie koło wyplatane, stanowiące część automatycznej instalacji. Dzięki niej BMC jako pierwszy producent na świecie wytwarza w zautomatyzowany sposób ramy karbonowe. Stuprocentowa automatyzacja jest przy tym równoznaczna z zachowaniem stuprocentowej jakości. Ze względu na perfekcję uzyskiwaną mimo produkcji seryjnej projektanci BMC wymyślili nazwę „the impeccable bike”, krótko „impec”, czyli „rower idealny”.
Rury bezszwowe
Produkcja ram karbonowych, wymagająca dotychczas żmudnej, ręcznej pracy, polegającej na zwijaniu, formowaniu i sklejaniu kolejnych warstw mat, przebiega obecnie w BMC jak w szwajcarskim zegarku. Każdy poszczególny element ramy jest przez „Stargate” zaplatany jako całość wokół tzw. formy pozytywowej. Ultracienkie nici nawinięte na ponad 100 szpul przebiegają z zawrotną prędkością przez koło wyplatające, błyskawicznie tworząc bezszwowe, elastyczne rury z włókien karbonowych. Nie da się zaprzeczyć, że ten etap wygląda poniekąd jak produkcja czarnych męskich skarpetek. Dotychczas technologia koła wyplatającego była znana przede wszystkim z produkcji lin stalowych, stosowanych przykładowo w kolejkach górskich. W przetwarzaniu karbonu jest to absolutne novum. W BMC nazwano tę technologię Load Specific Weave (LSW). To oznacza, że przy użyciu tego zaawansowanego technologicznie koła wyplatającego można wytwarzać materiały o różnej grubości, co pozwala uzyskać optymalny rozkład obciążeń. Ta innowacyjna metoda pozwala indywidualnie dostosować późniejsze rury do wymogów poszczególnej partii ram. Po wypleceniu tekstylia karbonowe są nasączane w foremnikach żywicą epoksydową i wstępnie utwardzane w formach negatywowych, które nadają rurom karbonowym ostateczną postać.
Stabilny proces suszenia
Po uformowaniu rury karbonowe poddaje się procesowi utwardzania i suszenia, co trwa, w zależności od grubości warstw, od 15 do 120 minut. Również tutaj niczego nie pozostawia się przypadkowi. Komory temperaturowe BINDER serii FED służą w BMC do utrzymania stabilnie suchego klimatu przy stałej wilgotności powietrza oraz temperaturze 80 °C. Gwarantują optymalne rezultaty utwardzania żywic epoksydowych. Również podczas finalnego montażu oraz uszlachetniania elementów ramy doskonale sprawdzą się komory temperaturowe BINDER. Podczas suszenia i utwardzania lakierów, nadruków i klejów montażowych komory temperaturowe BINDER serii FED odgrywają decydującą rolę. Dzięki pojemności wynoszącej od 53 do 400 l i potencjalnym temperaturom sięgającym nawet 300 °C można je doskonale dostosować do najróżniejszych wymogów. Mają też pewną zaletę szczególną: niskie zużycie energii. Dzięki warstwie izolacyjnej o grubości 60 mm komory temperaturowe BINDER gwarantują wyjątkowo niską emisję ciepła. Wysokogatunkowe produkty BINDER dos konale sprawdzają się w absolutnie nowatorskim zautomatyzowanym procesie produkcji ram karbonowych. W ciągu zaledwie czterech lat inżynierowie BMC postawili na nogi przełomową instalację.

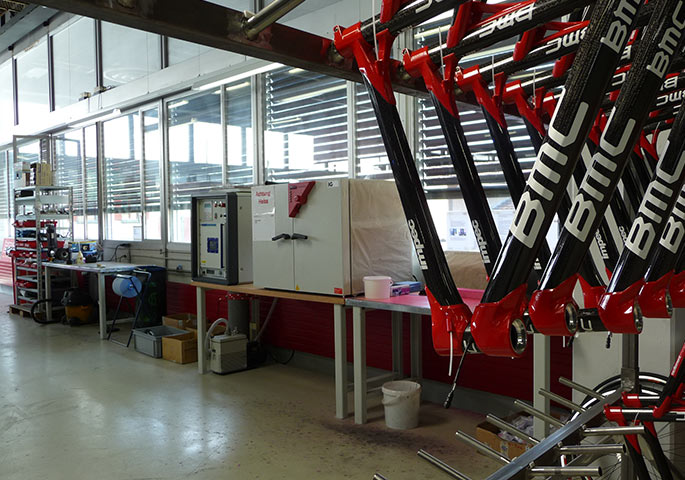
Zalety:
- Szybkie, równomierne suszenie
- Duży zakres temperatury
- Bogate wyposażenie seryjne
- Uzupełniające linie produktowe uwzględniające wilgotność, oświetlenie, CO2 lub próżnię
- Jakość „Made in Germany“
Obszar zastosowania:
- Przemysł elektryczny/elektroniczny
- Badania podstawowe / instytuty badawcze
- Produkcja tworzyw sztucznych