Case Study GEWO: The BINDER Chambers in the Clean Room
Tasks:
- Chambers must be suitable for clean room work
- It must be possible to achieve a high temperature range
- A controller must be available to record everything
- Easy operability because the employees are working in protective jumpsuits
BINDER solutions:
- Temperature range: Room temperature plus 15 °C to 200 °C
- APT.line™ preheating chamber technology
- Controller with time-segment and real-time programming
- 2 aluminum expansion racks
- Inert gas connection
- Shatterproof, spring-mounted safety glass panel
- Class 2 independent adjustable temperature safety device (DIN 12880) with visual alarm
- Computer interface: RS 422
- 2 relay outputs, 24 DC (max. 0.4 A)

If you visit the small Bavarian town of Hörlkofen near Erding, you might not necessarily expect a thriving, state-of-theart company with roughly 350 employees. This company is owned by the Woitzik family and has grown into a popular partner in the precision engineering industry in just 30 years. Renowned customers like Zeiss have come to rely on the high-quality products from Upper Bavaria.
Among these products are clever mechanical assemblies used in the semiconductor industry, which make it possible to manufacture processors for smartphones. These highly sensitive components have to function with precision and need to leave the manufacturer's site in an absolutely clean state. BINDER, based in Tuttlingen, Germany, offers the solution here. Thanks to its powerful vacuum drying chambers, these components can be delivered in a condition suitable for use in high vacuum.
Getting a glimpse at a part of the BINDER chambers at GEWO first requires gaining access to the clean room outfitted with a lot of technology. Master precision mechanical engineer Andreas Megele is there to welcome us today and provides us with clothing that must be worn to preserve cleanliness. Not one speck of dust is allowed to enter the absolute clean room, where up to 25 employees are busy cleaning the components. Processors and chips are sensitive. Contamination of a machine used in production can paralyze an entire production system.
A great deal of effort is required to get into the clean room. The requirements placed on employees are also high in these facilities. Here, eating and drinking are prohibited. Even the toilet is located outside of this area, meaning that you need to change clothes each time you leave the room.
The cleaning process for the components that will later bring a smartphone to life is also a rigorous one. The components go through pre-cleaning first, which is followed by precision cleaning. Later, they are plunged deep into the ultrasonic cleaning tank. The BINDER chamber, meanwhile, is waiting for the component, which is then dried for 48 hours at 100 degrees Celsius. This removes liquid from the pores. Any remaining surface contamination can thus be cleaned without liquids.
Alternatively or for certain components, two drying chambers are used. Megele says, however, “These specific components are best dried in a vacuum drying chamber. That is, after all, why the BINDER chambers are in the clean room." Because outgassing is not permitted in the clean room, the BINDER chambers were specifically prepared for this location. "This worked wonderfully," states Megele.
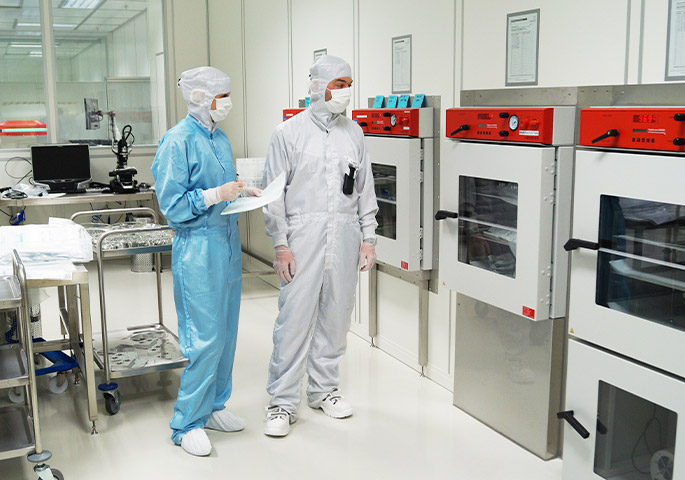
The BINDER chambers generally operate continuously and do so without any issues. Taking a look around the GEWO facility, you will find a 30-year-old BINDER chamber. While it might not be in the clean room, it is in use elsewhere. GEWO manufactures a great deal of different products. Smaller companies can bring an idea to the company in Upper Bavaria and product development will follow. That was the route taken by Thermo Fisher, a company for which GEWO makes measuring cells. These measuring cells are used in liquid analysis, such as for medications. This manufacturing
process uses a BINDER drying chamber required for adhesive curing. In two hours at a constant 60 degrees Celsius, the measuring cell is prepared so that it can be used effectively in the end.
Advantages of vacuum drying chambers:
- Fast, gentle drying
- Direct thermal transfer through large heat transfer plates
- Safe work thanks to proven safety concept
- Coordinated complete modular system with vacuum pump and module
