Case Study: BMC Racing Caronrahmen
Tasks and objectives:
- Drying and curing of formed carbon tubes
- Drying and curing varnishes, overprints and assembly adhesives
- Constant drying climate
- Constant atmospheric humidity
- Low energy consumption
- Low heat dissipation
- Easy operation
BINDER solutions:
- FED heating chamber with forced convection
- Homogenous temperature conditions
- Uniform air circulation with digitally adjustable fan
- Large temperature range of approx. 5 °C above ambient temperature to 300 °C
- Short heating up times
- Low heat dissipation due to 60 mm insulation
- Advanced timing functions

Carbon comes into play when something has to be extremely lightweight and highly stable. In Grenchen, Switzerland, automated manufacturing is used with the help of BINDER technology to produce carbon frames for racing bikes for the first time ever. In 2011, Australian Cadel Evens won the Tour de France on a BMC racing bike thanks to the enthusiastic support of his team members, who contested the world‘s most difficult stage race on carbon racing bikes. They call it „Stargate“ and what comes out of it almost seems to come from another planet. A wheel with a diameter larger than a person with outstretched arms produces one of the strongest and lightest materials known to man today: finely woven carbon – the wonder material of racing bike frames. Strictly speaking, „Stargate“ is a high-tech braiding machine and part of a complex automation system. The racing
bike manufacture BMC headquartered in Grenchen, Switzerland, manufactures the world‘s first carbon frames using a completely automated process. 100 percent automation is synonymous with 100 percent consistently high quality. With perfection in series production, its BMC designers have called it „the impeccable bike“ or „impec“ for short.
Seamless tube
Where carbon frames had to be painstakingly laminated, shaped and glued by hand from individual layers until now, production at BMC runs cleanly and smoothly like Swiss clockwork precision. Each part of the frame is woven in the „Stargate“ around the socalled positive core as a whole. More than 100 bobbins loaded with wafer-thin threads run through the braiding machine at breathtaking speeds to weave a seamless, flexible tube of carbon fibers in seconds. A certain similarity with a black stocking cannot be denied at this stage of production. Until now, braiding machine technology has primarily been known in the manufacture of steel cable such as that used for mountain railways or cable cars. In carbon processing, it is an absolute novelty. BMC calls its technology Load Specific Weave (LWS). The high-tech braiding machine is used to weave varying degrees of material thickness and load distributions. The innovative method allows you to manufacture frame tubes made-to-measure for each individual section of the frame. After the weaving process is completed, the carbon fabric is soaked in the molds with epoxy resin and pre-cured in negative forms that give the carbon tubes their final shape.
Uniform drying
After shaping, the carbon tubes must be cured and dried for 15 to 120 minutes depending on the wall thickness and size. Even here nothing is left to chance. BINDER heating chambers of the FED series ensure a uniform drying climate at BMC at constant humidity and a temperature of 80 °C. They provide the best possible conditions for curing the epoxy resin. BINDER heating chambers are even used during final assembly and finishing of the frame sections. When drying and curing lacquers, lettering and assembly adhesives, BINDER heating chambers of the FED series play a supporting role. With a capacity of 53 to 400 l and possible temperatures of up to 300 °C, they are ideally suited for the wide range of requirements. And they do one thing particularly well: save energy. Thanks to their 60 mm insulating layer, BINDER heating chambers exhibit extremely low heat dissipation.
Fleet-footed success
The high quality products from BINDER seamlessly integrate into the world‘s first automated production process of carbon frames. In just four years, BMC developers have got the pioneering facility up and running. It has been worth it: An impec carbon frame from BMC only weighs about 1 kg on average. How successful the overall concept would be in practice in just a short period of time may have even surprised BMC a little. The Swiss BMC racing team around the world champion Cadel Evans was able to compete at the Tour de France on an impec for the first time ever in 2010.

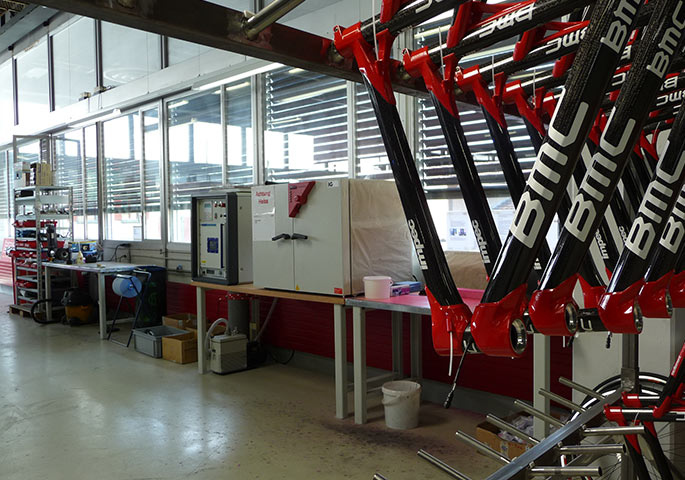
BINDER Products:
- Fast, even drying
- Wide temperature range
- Comprehensive standard equipment
- Additional product lines with humidity, light, CO2 or vacuum
- "Made in Germany" quality
Areas of application:
- Electronics / semiconductor industry
- Basic research / research institutes
- Plastics industry