Case Study TPE Kraiburg
Tasks and objectives:
- Precise maintenance of temperature in short-term and long-term tests
- Test results must be logged and transferred directly to the PC
- Units should be stackable
- Heating chambers must be suitable for special testing
BINDER solutions:
- Temperature range: plus ten to 300 °C
- Up to 30% lower energy consumption compared to conventional units on the market
- High temperature accuracy
- Forced convection
- Controller with LCD display
- Electromechanical control of the exhaust air flap
- Two chrome-plated racks
- Ergonomic handle design
- USB port for recording data

TPE is a versatile product
The company Kraiburg TPE from Waldkraiburg in Germany produces thermoplastic elastomers, an extremely innovative product that we will all have come across at some point in our day-today lives.
From soft toothbrush handles to children's toys and haptic elements in tools – thermoplastic elastomers from KRAIBURG TPE provide real added value in all kinds of different products. TPEs from Waldkraiburg are also in high demand in the automotive industry, where they are used in vehicle interiors and exteriors and in engine-related applications for a number of well-known car manufacturers.
For example, TPE compounds make the controls comfortable to handle, provide glazing encapsulation with outstanding
weather resistance, and can be used as sealing elements with high temperature resistance in the engine compartment.
The granulate, which can be easily processed by the end customer, does however need to be checked on a regular basis to assess its resistance levels. How do the thermoplastic elastomers change when they are exposed to certain media such as greases or water? How does the material react to high temperatures in conjunction with this substance? These are just two of the fascinating questions that TPE specialist Robert Klier deals with on a day-to-day basis. And this is where Tuttlingen-based company BINDER comes into play. The company provides the laboratory team leader with the equipment required for extensive testing. “We tried out a few different simulation chambers in the past, but we decided to stick with BINDER. They really are top-quality products – we now have 16 drying and heating chambers, one dynamic climate chamber, and one vacuum drying chamber in our laboratory,” says Klier, who requires the highest degree of accuracy in his measurements.
At the end of a test run, the key criterion for Klier is that the interference factors have not resulted in any changes. Together with his team, and with the help of the BINDER chambers, the laboratory team leader also simulates the processing of the thermoplastic elastomers at the end customer's site. “In this process, we check what happens when soft TPEs and hard materials come together – for example, in the case of a toothbrush. The adhesion between TPEs and hard thermoplastics comes not from a chemical bond, but from attractive
intermolecular forces and a mechanical anchoring of macromolecules of both components,” explains the specialist. Furthermore, at KRAIBURG TPE, every raw material undergoes in-depth testing on arrival and can only be used for production following internal approval. The BINDER heating chambers are used in particular for testing compression set, swelling behavior, and aging. “The standard tests in a drying and heating chamber (FD) take between 24 and 72 hours at 70 to 150 °C. This often involves aging the materials at an accelerated rate,” reports Klier. Special testing – when a product is to be changed or further developed, for example – is carried out in continuous operation.
This type of testing can take up to 1000 hours at 120 °C. Klier: “In the case of special testing, we need to fit the heating chambers with test equipment which we produce on a very individual basis. The chambers provide the ideal environment for equipment of this kind. Tests like this are used for the automotive industry in particular.” This was not the only advantage that won over KRAIBURG TPE – the accuracy of the BINDER units was also a crucial factor. “KRAIBURG TPE is known on the market as a specialist for thermoplastic elastomers. In order to build up our expertise, we rely entirely on high-quality suppliers and partners. We are happy to have found an expert partner for heating chambers in BINDER,” adds the laboratory team leader.
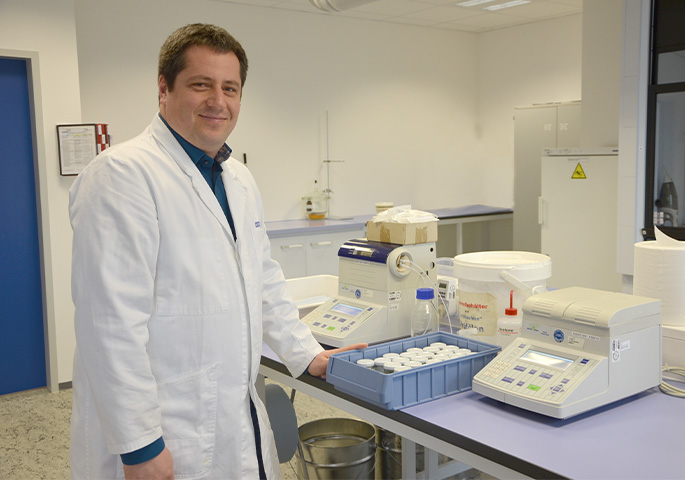

Advantages of drying and heating chambers
- Safe and accurate tests
- “Made in Germany” quality
- Two materials can be tested at the same time in one chamber
- Special testing of all kinds possible
- Easy to use: good insertion technology and a very reliable controller
- Easy to look after
- Networking: software can be analyzed quickly